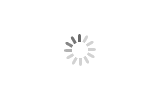
- ZK
- China
- 2-7days
- 200pcs/day
A leading international vector control algorithm to achieve high-performance, high-precision motor drive control, to improve reliability and suitability of the product for the environment at the same time, strengthen the customer ease of use and design industry specialization, more optimization, application more flexible, more stable performance.
Variable speed drive introduction:
S100 series is a high performance General Purpose Frequency Inverter with current vector control. It mostly used to control and adjust the speed and torque of the 3 phase induction motor and also PMSM. It adopts mature platform of software and hardware with a high level standard design.
Specification:
Single phase, 220V, 0.4kw to 2.2kw. Three phase, 220V, 0.75kw to 132kw
Three phase, 380V/660V/1140V, 0.75 to 800kw.
Key product feature:
1. High performance flux vector control for IM and PMSM
2. Excellent quick response with vector control
3. High starting torque even under low speed.
4. Torque limit for machine safety protection
5. Rapid current limit, up to 20 kinds protection function.
6. Latest generation Fuji IGBT modules using
1. IGBT module using: Using the latest generation of INFINEON/FUJI brand which is the best choose for inverter application. | 2. Stronger protection: All-around test the components and temperature rise. Output ground short circuit protection,relay (contactor) actuation fault protection,brake circuit over current, brake tube over load etc protection to improve the system security. |
![]() | ![]() |
3. Conformal coating with reliability and stabilization: Professional design with three proofing coating process,good EMC performance. | 4. Optimizing hardware design to reduce the fault: PCB board 4 layer design to reduce “fly” wire and improve stability. 3 current sensor enhance the output protection. |
![]() | ![]() |
5. Longer life running:Quality components using to guarantee the inverter to have a longer life for work | 6. Wide voltage design: Full consideration of the grid voltage fluctuation and unbalance. |
![]() | ![]() |
Technical Information:
Items | Specification | |||
Control mode | Control mode | V/F control | Sensorless in open loop | Close loop vector control |
Starting torque | 0.5Hz 150% | 0.5Hz 180% | 0.00Hz 180% | |
Speed adjust range | 0: 50 | 1:100 | 1:1000 | |
Speed stabilizing precision | ±1% | ±0.1% | ±0.02% | |
Torque precision | NO | NO | ±5% | |
Motor type | General induction motor permanent magnet synchronous motor (PMSM ) | |||
Function design | Highest frequency | General vector control :320Hz V/f control: 3200Hz | ||
frequency resolution | Digital setting: 0.01Hz Analog setting:maximum×0.025% | |||
Carrier frequency | 0.5K~16KHz, the carrier frequency can be adjusted by temperature automatically | |||
Frequency reference setting method | Digital of Control panel, analog AI1, AI2, potentiometer of control panel, UP/DN control, communication, PLC pulse frequency | |||
Acceleration./deceleration characteristic | Linear curve and S curve accel. /decel. mode, range of time: 0.0 to 65000S. | |||
V/F curve | 3 mode: linear, multiple points, N Power | |||
V/F separation | 2 times separation: totally separation, half separation | |||
DC braking | DC braking frequency: 0.0 to 300Hz, DC braking current: 0.0% to 100% | |||
Braking unit | Standard built in for up to 4T22G (22kw), optional built it for 4T30G~4T110G (30kw to 110kw), external built for above 4T160kw . | |||
Jog function | Job frequency range: 0.0 to 50.0Hz, the acceleration and deceleration time of Jog | |||
Configured PID function | Easy to perform pressure, flow, temperature close loop control. | |||
PLC multiple speed | To achieve 16 segment speed running through built in PLC or terminal control | |||
Common Dc bus | Multiple drives use one DC bus for energy balance. | |||
Auto voltage regulation (AVR) | Enable to keep output voltage constant when grid fluctuation | |||
Over load tolerance capability | G type model: 150% rated current for 60s, 180% rated current for 3s, P type Model: 120% rated current for 60s, 150% rated current for 3s. | |||
Stall protection control when over current, over voltage | Carry out limiting automation for running current, voltage to prevent over current, over voltage frequently | |||
Rapid current limit function | Minimize the IGBT module broken to protect the AC Drive, maximum reduce the over current fault. | |||
Torque limit and torque control | "Excavator" characteristics , torque limit automatically during motor running. Torque control is available in close loop vector control mode. | |||
Features | Friendly interface | Display “Hello” when power on. | ||
Multiple function key JOG button | It can set for Forward Jog, reverse Jog, forward/reverse switch | |||
Timing control function | A total running time and total running time calculating | |||
2 group motor parameters | To achieve two motor switchover freely, control mode is selectable | |||
Motor over heat protection | Accepting motor temperature sensor signal input via AI1 terminals. | |||
Multiple kinds encoder * | Compatible collector PG, differential PG, and rotary transformer Encoder( resolver). | |||
Command source | Control panel, control terminals, series communication, switch freely. | |||
Frequency source | Digital setting, analog current/voltage, pulse setting, serial communication, main and auxiliary combination. | |||
Protection function | Short circuit detect when power on, input/output phase loss, over voltage, over current, under voltage, over heat, over load protection. | |||
Environment | Application site | Indoor, free of exposure to sunlight, no dusty, no corrosive, no inflammable gas, no oil and water vapor, and water dipping | ||
Altitude | Lower 1000m | |||
Environment temperature | -10℃~+40℃, power derated for 40~50℃, rated current derated 1% for 1℃ increasing. | |||
humidity | Less than 95%, no water condense. | |||
storage | -40~+70℃ | |||
IP degree | IP20 |